Maximize Warehouse Storage Efficiency-Tips based on Warehouse Racking in Dubai
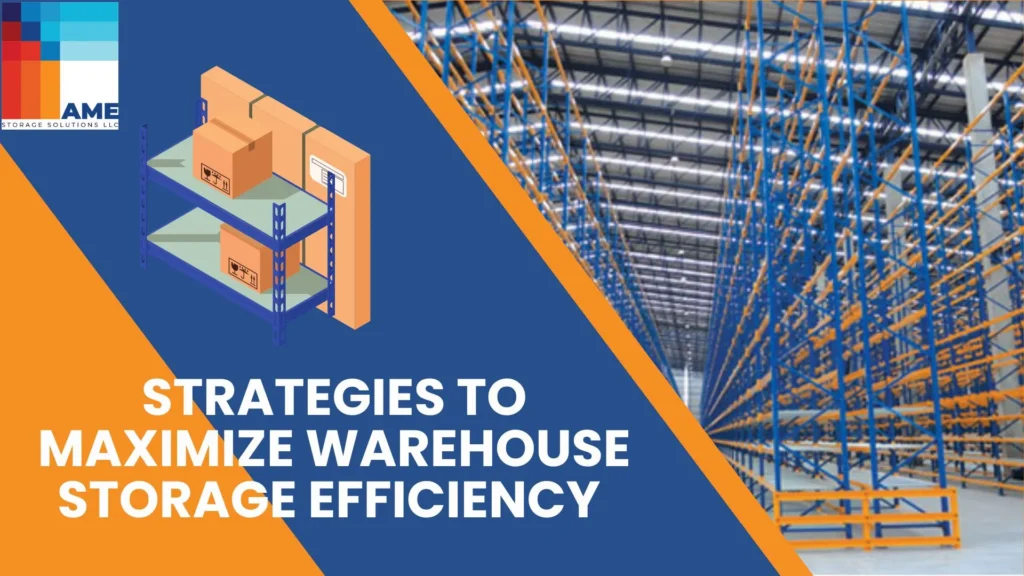
Maximizing warehouse storage efficiency is crucial for businesses to optimize their operations and minimize costs. Here are some tips to increase warehouse storage efficiency, based on warehouse racking in Dubai.
Implement an Effective Warehouse Layout
Designing an effective warehouse layout plays a crucial role in maximizing storage efficiency. Here are some key considerations to implement , by taking the example of many leading racking suppliers in UAE :
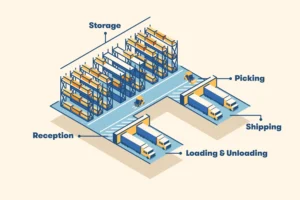
-
- Analyze Space Requirements: Begin by assessing the available warehouse space and understanding your storage needs. Consider factors such as the size and volume of your inventory, the types of products (bulk, pallets, small items), and any specialized storage requirements (temperature-controlled, hazardous materials).
-
- Determine Storage Zones: Divide your warehouse into functional zones based on the nature of your operations. Common zones include receiving, storage, picking, packing, and shipping areas. Ensure clear pathways and sufficient space for movement between these zones.
-
- Optimize Flow: Plan the flow of goods within the warehouse to minimize travel distances and streamline operations. A logical flow typically involves receiving at one end, with products moving through storage, picking, packing, and shipping areas in a sequential manner. Minimize bottlenecks and optimize the workflow to enhance efficiency.
-
- Consider Accessibility: Place frequently picked items closer to the packing and shipping areas to minimize travel time. High-demand products should be easily accessible to ensure faster order fulfillment. Reserve prime locations for fast-moving SKUs to increase picking efficiency.
-
- Use Vertical Space: Utilize the vertical space by installing tall storage systems such as pallet racking or mezzanines. Vertical storage allows for better space utilization while keeping products easily accessible. Consider the weight capacity, safety regulations, and proper equipment (such as forklifts) for vertical storage.
-
- Implement Slotting Strategy: Apply a slotting strategy to assign appropriate storage locations based on product characteristics, demand, and picking frequency. Group similar products together to optimize picking routes. Consider factors like product size, weight, and turnover rate when determining the ideal storage locations.
-
- Safety Considerations: Ensure compliance with safety regulations and create a safe working environment. Clearly mark walkways, use safety barriers, and install proper lighting for visibility. Place safety equipment, such as fire extinguishers and first aid kits, at easily accessible locations.
-
- Embrace Technology: Implement warehouse management systems (WMS) and automated solutions to optimize storage efficiency. WMS can track inventory levels, manage picking routes, and provide real-time data for better decision-making. Consider technologies like barcode scanners, RFID systems, or automated storage and retrieval systems (AS/RS) for faster and more accurate inventory management.
-
- Flexibility and Scalability: Design the layout to accommodate future growth and changing business needs. Opt for modular storage solution systems that can be easily reconfigured or expanded as required. Plan for flexibility to adapt to new products, seasonal demands, or operational changes.
-
- Continuous Improvement: Regularly review and optimize your warehouse layout. Analyze operational data, seek feedback from staff, and identify areas for improvement. Implement changes based on the findings to continually enhance storage efficiency and overall warehouse performance.
Utilize Vertical Space
Using vertical space effectively is an essential strategy for maximizing warehouse storage efficiency. Here are some key approaches to make the most of the vertical space in your warehouse:
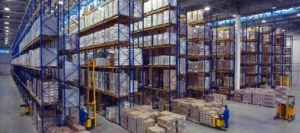
-
- Install Tall Storage Systems: Invest in tall storage systems such as pallet racking, which allows for stacking products vertically. These racks provide multiple levels of storage, utilizing the full height of your warehouse. Choose racking systems that are sturdy, adjustable, and designed to handle the weight and size of your inventory.
-
- Consider Mezzanine Floors: Mezzanine floors are intermediate floors installed between existing levels, effectively doubling the available space. Mezzanines provide additional storage areas without expanding the warehouse footprint. They can be used for storing smaller items, creating office space, or adding more picking locations.
-
- Utilize Vertical Carousels or Lift Modules: Vertical carousels and lift modules are automated systems that store items vertically and retrieve them when needed. These systems use the vertical height of the warehouse and can significantly increase storage capacity. They are particularly useful for storing smaller, high-demand items or items with high turnover rates.
-
- Implement Vertical Conveyors: Vertical conveyors, such as vertical lift modules or vertical reciprocating conveyors, transport goods vertically between different levels of the warehouse. They efficiently move items to higher storage levels or bring them down when needed, saving time and effort in manual handling.
-
- Use Stackable Containers or Bins: Choose stackable containers or bins that can be easily stacked on top of each other. Optimize the stacking configuration by ensuring stability and proper weight distribution. This approach is particularly effective for storing smaller items or parts that can be easily organized and accessed when needed.
-
- Implement Cantilever Racks: Cantilever racks are designed for storing long and bulky items, such as pipes, lumber, or steel bars. They have arms that extend from vertical columns, allowing easy access to stored items. Cantilever racks optimize vertical space by accommodating items of various lengths and sizes.
-
- Consider Push-Back Racking: Push-back racking systems utilize inclined rails and carts that allow for multiple pallets to be stored on different levels. As new pallets are loaded, they push the previously loaded pallets further back along the rails. This system maximizes storage density and facilitates efficient inventory rotation.
-
- Ensure Safety and Accessibility: When utilizing vertical space, it is crucial to prioritize safety and accessibility. Use appropriate equipment, such as forklifts or reach trucks, to safely handle items stored at higher levels. Ensure that all storage systems comply with safety standards and that employees receive proper training in operating equipment and working at heights.
-
- Optimize Inventory Placement: Strategically plan the placement of inventory based on demand, turnover rates, and accessibility. Frequently accessed items should be placed on lower levels or in easily reachable positions, while slower-moving items can be stored at higher levels.
-
- Regular Maintenance and Inspections: Regularly inspect and maintain vertical storage systems to ensure they are in proper working condition. Check for any signs of damage, wear and tear, or structural issues. Conduct routine inspections to identify and address potential safety hazards.
Implement Cross-Docking
Implementing cross docking in a warehouse can streamline operations and reduce storage requirements. Here are the key steps to implement cross docking effectively:
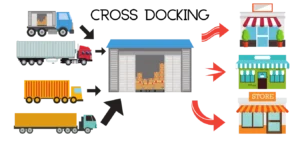
-
- Assess Product Eligibility: Evaluate your inventory to identify products suitable for cross docking. Typically, these are fast-moving items with a high turnover rate, pre-packaged goods, or products with consistent demand. Cross docking is most effective when applied to items that require minimal processing or customization before shipment.
-
- Plan Receiving and Shipping Areas: Designate specific areas in your warehouse for receiving incoming shipments and preparing outbound orders. These areas should be in close proximity to each other to minimize travel time and facilitate efficient transfer of goods. Ensure that the layout allows for smooth flow of materials through the cross docking process.
-
- Collaborate with Suppliers and Carriers: Establish clear communication channels with suppliers and carriers to coordinate the timing of inbound shipments. Align delivery schedules with your cross docking operations to ensure that goods arrive when they are needed for immediate shipment. This collaboration is essential for a seamless cross docking process.
-
- Streamline Documentation and Labeling: Implement electronic data interchange (EDI) or other automated systems to streamline documentation and reduce manual handling of paperwork. Utilize barcoding or RFID technology to label products accurately and track them throughout the crossdocking process. This ensures efficient handling and minimizes errors.
-
- Plan Workforce and Equipment: Assign dedicated personnel to handle cross docking activities, including receiving, sorting, and loading. Ensure that they are well-trained and equipped with the necessary tools, such as forklifts, pallet jacks, or conveyors, to move goods swiftly and safely. Optimize staffing levels based on the volume of cross docking operations.
-
- Prioritize Sorting and Consolidation: As goods arrive, sort them immediately based on their destination or outbound orders. Consolidate items with similar destinations to streamline the loading process. This step requires efficient coordination and accurate product tracking to ensure the right products are grouped together for outbound shipments.
-
- Minimize Handling Time: Cross docking aims to minimize storage time. Therefore, it is crucial to expedite the transfer of goods from the receiving area to the outbound shipping area. Focus on optimizing processes, such as palletizing, labeling, and quality checks, to reduce handling time and expedite the movement of goods.
-
- Utilize Technology and Automation: Implement technology solutions such as warehouse management systems (WMS) and transportation management systems (TMS) to streamline cross docking operations. These systems provide real-time visibility into inventory, automate processes, and optimize routing and scheduling for efficient cross docking.
-
- Continuous Monitoring and Improvement: Regularly monitor and analyze key performance indicators (KPIs) related to cross docking, such as dock-to-stock cycle time, order accuracy, and shipment timeliness. Identify bottlenecks or areas for improvement and make adjustments to enhance the efficiency and effectiveness of cross docking operations.
-
- Collaborate with Stakeholders: Foster collaboration and open communication with all stakeholders involved in the cross docking process, including suppliers, carriers, and internal teams. Regularly review performance, share feedback, and identify opportunities for further optimization.
Use FIFO and LIFO Principles
Implementing the first-in, first-out (FIFO) and last-in, first-out (LIFO) principles in your warehouse can help optimize inventory management and storage efficiency. Here’s how you can utilize these principles effectively:
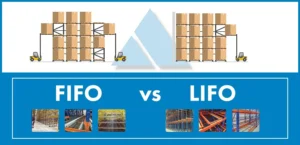
-
- FIFO (First-In, First-Out):
-
- Inventory Rotation: Arrange your inventory in a way that older stock is used or shipped out first. This principle is especially important for products with expiration dates or those prone to obsolescence.
-
- Labeling and Tracking: Clearly label products with manufacturing or arrival dates and implement a tracking system to ensure proper rotation. This helps in identifying and picking items based on their arrival sequence.
-
- Stock Placement: Organize your storage areas to allow easy access to the oldest stock. Place newly received items behind or above older stock to ensure that the oldest items are picked first.
-
- LIFO (Last-In, First-Out):
-
- Stock Placement: With LIFO, the most recently received items are used or shipped out first. Place the newest stock in the most accessible areas of your warehouse to facilitate efficient picking.
-
- Monitoring Expiration Dates: If your inventory consists of perishable goods, closely monitor expiration dates to prevent wastage. Ensure that the newest stock is easily visible and regularly checked for expiration.
-
- Stock Rotation: While LIFO is often used for non-perishable goods or when there are no specific date requirements, it’s still important to periodically assess stock levels and rotate inventory to avoid items becoming obsolete or outdated.
-
- Hybrid Approach:
-
- Depending on your inventory mix and business requirements, you can implement a combination of FIFO and LIFO principles. This approach allows for flexibility based on the characteristics of different product categories.
-
- Assign specific items or product groups to either FIFO or LIFO based on their nature, demand patterns, or customer requirements. This ensures that the most appropriate principle is applied to each category.
-
- Regularly review and adjust your inventory management strategy to align with changes in demand, market trends, or shifts in product priorities.
Optimize Slotting
Optimizing slotting in your warehouse involves strategically assigning storage locations to maximize efficiency and streamline operations. Here are some steps to optimize slotting effectively:
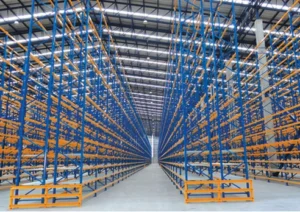
-
- Analyze Inventory Characteristics: Conduct a thorough analysis of your inventory to understand its characteristics, including size, weight, fragility, turnover rate, and special storage requirements (such as temperature or humidity control). Categorize items based on these factors to inform your slotting strategy.
-
- Classify Products: Utilize techniques like ABC analysis or velocity analysis to classify products based on their demand, value, or turnover rate. This classification helps determine the most suitable slotting strategy for each product category.
-
- Determine Picking Frequencies: Analyze order patterns and picking frequencies to identify fast-moving items or high-demand SKUs. These items should be placed in easily accessible locations, closer to picking and shipping areas, to minimize travel time and improve efficiency.
-
- Optimize Aisle Widths: Consider the width of your warehouse aisles. Narrower aisles allow for more storage space but may limit maneuverability, while wider aisles provide more flexibility but reduce storage density. Find a balance that optimizes space utilization and allows for efficient movement of equipment and personnel.
-
- Implement Slotting Techniques:
-
- Cubic Space Utilization: Make use of vertical space by storing items in taller storage systems, maximizing storage capacity.
-
- Zone Picking: Group items with similar picking requirements in dedicated zones. This reduces travel time and consolidates picking activities, improving productivity.
-
- Cross-Docking Zones: Designate specific areas for cross-docking operations to streamline the flow of goods and reduce storage requirements.
-
- Golden Zone Slotting: Place high-demand or high-value items within the “golden zone” or prime picking area, which is easily accessible and saves time during order fulfillment.
-
- Product Families: Group related products together to optimize picking routes and minimize travel time within the warehouse.
-
- Optimize Placement Rules: Develop placement rules based on the characteristics and demand patterns of your products. Consider factors such as weight limits, fragility, expiration dates, or compatibility. Ensure that the placement rules are communicated and followed consistently by warehouse staff.
-
- Leverage Technology: Utilize warehouse management systems (WMS) or inventory management software to automate slotting decisions. These systems can analyze data, suggest optimal storage locations, and provide real-time insights into inventory status.
-
- Regularly Review and Adjust: Continuously monitor and analyze warehouse performance metrics, such as order fulfillment rates, picking accuracy, and travel distances. Regularly review and adjust your slotting strategy based on changing product demands, business priorities, and customer requirements.
-
- Employee Training: Train warehouse staff on the importance of slotting optimization and the specific slotting strategies in place. Provide them with the necessary knowledge and skills to effectively execute the slotting strategy and maintain organized storage areas.
-
- Continuous Improvement: Foster a culture of continuous improvement within your warehouse. Encourage feedback from employees and regularly evaluate the effectiveness of your slotting strategy. Seek opportunities to enhance efficiency, reduce errors, and adapt to changing business needs.
Train Warehouse Staff
Training warehouse staff is crucial for ensuring smooth operations, optimizing efficiency, and maintaining a safe working environment. Here are some key steps to effectively train your warehouse staff:
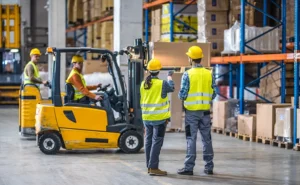
-
- Develop a Training Plan: Start by creating a comprehensive training plan that outlines the topics, goals, and timeline for each training session. Identify the specific skills and knowledge areas that need to be covered, such as equipment operation, safety procedures, inventory management, and warehouse processes.
-
- Provide Orientation and Onboarding: Begin with a thorough orientation program for new hires. Introduce them to the company culture, safety protocols, and the layout of the warehouse. Provide an overview of the various departments and their functions. Assign a mentor or buddy to help new employees acclimate to their roles.
-
- Safety Training: Emphasize safety as a top priority in the warehouse. Train staff on proper handling of equipment, including forklifts, pallet jacks, and conveyors. Teach them about personal protective equipment (PPE) requirements, emergency procedures, and how to identify and report safety hazards. Conduct regular safety drills and refresher training to reinforce safe practices.
-
- Equipment Training: Provide hands-on training on the use and maintenance of warehouse equipment. Train staff on how to operate forklifts, reach trucks, and other material handling equipment safely and efficiently. Emphasize proper loading, unloading, and stacking techniques to prevent damage to products and equipment.
-
- Inventory Management Training: Educate staff on inventory management processes, including receiving, storing, picking, and shipping. Teach them how to accurately track inventory levels, use barcode scanners or RFID systems, and follow proper labeling and documentation procedures. Highlight the importance of accuracy and attention to detail in maintaining inventory integrity.
-
- Process and Workflow Training: Train employees on the specific processes and workflows within your warehouse. This includes order fulfillment, picking and packing procedures, cross-docking, and any specialized operations unique to your business. Emphasize the importance of efficiency, accuracy, and teamwork in executing these processes.
-
- Continuous Improvement and Problem-Solving: Foster a culture of continuous improvement by providing training on problem-solving techniques. Teach staff how to identify bottlenecks, analyze workflow inefficiencies, and propose solutions. Encourage them to contribute ideas for process improvements and provide feedback on current practices.
-
- Communication and Collaboration: Emphasize effective communication and collaboration among warehouse staff. Train them on how to use communication tools like two-way radios or warehouse management systems to coordinate tasks and share information. Encourage open dialogue, active listening, and teamwork to enhance productivity and minimize errors.
-
- Cross-Training Opportunities: Provide opportunities for cross-training to enhance versatility and flexibility among warehouse staff. This allows employees to gain exposure to different roles and develop a broader understanding of warehouse operations. Cross-training also helps with filling in for absences or managing peak periods effectively.
-
- Ongoing Training and Development: Remember that training is an ongoing process. Schedule regular refresher courses, workshops, or toolbox talks to reinforce knowledge, address emerging challenges, and introduce new techniques or technologies. Stay updated on industry trends and incorporate relevant training modules to keep your staff informed and motivated.
Regularly Review and Improve
Regularly reviewing and improving warehouse operations is essential for maintaining efficiency, optimizing processes, and adapting to changing business needs. Here are some key steps to regularly review and improve your warehouse, based on situations of warehouse racking in Dubai:
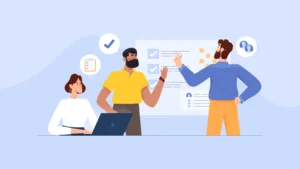
-
- Performance Metrics: Establish key performance indicators (KPIs) to measure warehouse performance. Track metrics such as order fulfillment rate, inventory accuracy, on-time delivery, picking and packing accuracy, and equipment utilization. Regularly review these metrics to identify areas for improvement and track progress over time.
-
- Data Analysis: Collect and analyze data related to warehouse operations. Utilize warehouse management systems (WMS) or other analytics tools to gain insights into inventory levels, order patterns, process bottlenecks, and resource utilization. Use this data to identify inefficiencies and make informed decisions for improvement.
-
- Continuous Improvement Culture: Foster a culture of continuous improvement among warehouse staff. Encourage them to actively participate in identifying areas for improvement, sharing ideas, and implementing process enhancements. Establish channels for collecting feedback and suggestions and recognize and reward innovative ideas.
-
- Process Mapping and Streamlining: Conduct process mapping exercises to visualize and understand the flow of materials and information within the warehouse. Identify areas of waste, redundant tasks, and bottlenecks. Streamline processes by eliminating non-value-added activities, improving workflow, and reducing cycle times.
-
- Cross-Functional Collaboration: Encourage collaboration and communication among different departments or teams involved in warehouse operations. Collaborate with other departments, such as procurement, sales, or customer service, to gain insights into customer requirements, demand forecasting, and inventory planning. Identify opportunities for synergy and implement cross-functional initiatives.
-
- Technology Integration: Regularly assess the effectiveness of your technology solutions, such as WMS, inventory management systems, or automation tools. Stay informed about advancements in warehouse technology and evaluate if any upgrades or enhancements can improve efficiency and accuracy. Leverage emerging technologies like artificial intelligence, robotics, or Internet of Things (IoT) for enhanced data visibility, automation, and optimization.
-
- Employee Training and Development: Continuously invest in the training and development of warehouse staff. Provide regular training sessions to refresh knowledge, introduce new processes or technologies, and enhance skills. Offer cross-training opportunities to develop multi-skilled employees who can fill various roles and adapt to changing demands.
-
- Supplier and Partner Collaboration: Engage in open communication and collaboration with suppliers and logistics partners. Regularly review performance, service levels, and contractual agreements. Seek feedback and identify areas where improvements can be made collaboratively to enhance overall supply chain efficiency
-
- Customer Feedback and Satisfaction: Regularly seek feedback from customers regarding their experience with order fulfillment, delivery accuracy, and overall satisfaction. Analyze customer feedback to identify areas of improvement and align warehouse processes with customer expectations.
-
- Lean and Six Sigma Principles: Consider implementing lean and Six Sigma principles to eliminate waste, reduce variation, and continuously improve processes. Apply lean tools like 5S (Sort, Set in Order, Shine, Standardize, Sustain) to maintain a clean and organized workspace. Utilize Six Sigma methodologies to identify and eliminate defects or errors in warehouse operations.
Use Optimal Storage Systems
Using optimal storage systems in your warehouse can greatly improve efficiency, maximize storage capacity, and enhance accessibility. Here are some examples of optimal storage systems you can consider implementing:
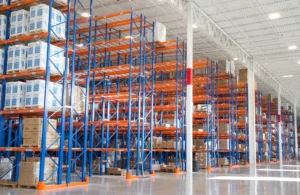
-
- Pallet Racking: Pallet racking systems are commonly used in warehouses and provide efficient storage for palletized goods. Options include:
-
- Selective Racking: Ideal for fast-moving products with high turnover rates. It allows direct access to each pallet.
-
- Double Deep Racking: Increases storage density by placing two pallets deep on each rack level.
-
- Drive-in/Drive-through Racking: Suitable for storing large quantities of homogeneous products with low turnover. Forklifts drive directly into the rack structure to deposit or retrieve pallets.
-
- Push-back Racking: Allows multiple pallets to be stored in a deep lane, with a last-in, first-out (LIFO) retrieval system.
-
- Shelving Systems: Shelving systems are versatile and can accommodate a wide range of products. Consider:
-
- Adjustable Shelving: Allows for easy customization to fit different product sizes and provides flexibility for future changes.
-
- Mobile Shelving: Compact storage solution that maximizes space utilization by eliminating fixed aisles. Shelves are mounted on mobile carriages that move along tracks.
-
- Carton Flow Shelving: Suited for high-volume order picking operations. Products are loaded from the back of the shelving unit and flow forward for easy access.
-
- Mezzanine Systems: Mezzanines create additional storage space by utilizing vertical height. They are constructed as an intermediate level between the floor and ceiling. Mezzanines are suitable for storing lightweight items or as additional workspace.
-
- Automated Storage and Retrieval Systems (AS/RS): AS/RS systems automate the process of storing and retrieving items, improving efficiency and reducing labor requirements. Options include:
-
- Vertical Lift Modules (VLM): Utilize vertical height by storing items in trays or bins that are automatically delivered to the operator.
-
- Automated Vertical Carousels: Consist of rotating shelves that bring items to the operator for picking or replenishment.
-
- Automated Guided Vehicles (AGVs): Mobile robots that autonomously transport items within the warehouse.
-
- Compact Storage Systems: Compact storage systems optimize space utilization by minimizing aisle space. Examples include:
-
- Mobile Racking: The racks are mounted on carriages that move sideways to create an access aisle when needed.
-
- Vertical Carousel Systems: Consist of rotating shelves that bring items to the operator. Suitable for small parts and high-speed picking operations.
-
- Cantilever Racking: Designed for storing long and bulky items such as lumber, pipes, or steel bars. Cantilever racks have arms that extend from vertical columns, providing easy access and flexibility for varying product lengths.
-
- Flow Racking: Flow racking systems use gravity to move products from the loading end to the picking end. This maximizes space utilization and ensures efficient stock rotation. Options include:
-
- Gravity Flow Racks: Products flow on inclined rollers or wheels, automatically moving forward as items are removed.
-
- Pallet Flow Racks: Pallets are loaded from one side and flow smoothly to the picking side using gravity.
When selecting optimal storage systems, consider factors such as the characteristics of your products, storage density requirements, order fulfillment processes, and available warehouse space. Assess your specific needs and consult with storage system experts to determine the most suitable solutions for your warehouse.
Employ Inventory Management System
Employing an inventory management system (IMS) is crucial for efficient warehouse operations and effective inventory control. Here are the key benefits and features of an inventory management system:
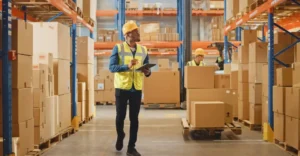
-
- Inventory Tracking: An IMS allows you to accurately track and monitor your inventory levels in real-time. It provides visibility into stock quantities, locations, and movement throughout the warehouse. This helps prevent stockouts, overstocking, and improves inventory accuracy.
-
- Demand Forecasting: Many IMSs offer demand forecasting capabilities by analyzing historical data, sales trends, and seasonality. This helps you make informed decisions about inventory replenishment, production planning, and demand fulfillment.
-
- Order Management: An IMS streamlines the order management process, enabling efficient order processing, fulfillment, and tracking. It automates order entry, generates pick lists, and tracks order status from picking to shipping.
-
- Replenishment Planning: With an IMS, you can set reorder points and define reorder quantities based on inventory levels, lead times, and desired safety stock. The system can automatically generate purchase orders or transfer requests to maintain optimal stock levels.
-
- Barcode/RFID Integration: IMSs often support barcode or RFID scanning, allowing for efficient and accurate tracking of inventory movements. This reduces manual data entry errors and speeds up processes such as receiving, picking, and cycle counting.
-
- Lot and Serial Number Tracking: For industries that require lot or serial number tracking, an IMS enables you to associate these identifiers with specific inventory items. This ensures traceability, facilitates recalls, and helps manage expiration dates or warranty information.
-
- Warehouse Optimization: IMSs can optimize warehouse operations by suggesting optimal storage locations, optimizing picking routes, and maximizing space utilization. This improves efficiency and reduces travel time for warehouse staff.
-
- Reporting and Analytics: An IMS provides comprehensive reporting and analytics capabilities. You can generate reports on inventory levels, turnover rates, stock valuation, and other key metrics. These insights enable data-driven decision-making and identify areas for improvement.
-
- Integration with Other Systems: An IMS can integrate with other business systems such as ERP (Enterprise Resource Planning) software, sales platforms, or logistics providers. This facilitates seamless data flow, improves coordination, and eliminates manual data entry across systems.
-
- Mobile Accessibility: Many modern IMSs offer mobile applications or web-based interfaces, allowing warehouse staff to access and update inventory information from mobile devices. This enhances flexibility, enables real-time data updates, and supports mobile barcode scanning.
Adopt ABC Analysis
Adopting ABC analysis is a valuable technique for optimizing inventory management and focusing resources on high-value items. ABC analysis categorizes inventory items into three groups based on their value and importance. Here’s how to implement ABC analysis in your warehouse:
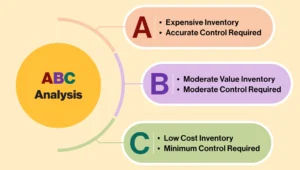
-
- Gather Data: Collect data on the sales history, unit costs, and other relevant information for each inventory item. This data will be used to determine the value and importance of each item.
-
- Calculate Annual Usage Value: Calculate the annual usage value for each item by multiplying the unit cost by the annual demand or sales quantity. The annual usage value represents the total value of sales or consumption for each item in a given period.
-
- Rank Items: Sort the items in descending order based on their annual usage value. This ranking will help determine which items have the highest value and impact on your business.
-
- Define Categories: Divide the items into three categories: A, B, and C, based on their ranking and cumulative usage value. The categorization can be determined based on a percentage breakdown, such as:
-
- Category A: The top 20% of items with the highest annual usage value. These items typically account for a significant portion of your sales or consumption and require close monitoring and rigorous control.
-
- Category B: The next 30% of items that have a moderate annual usage value. These items have moderate importance and should receive reasonable attention and control.
-
- Category C: The remaining 50% of items with the lowest annual usage value. These items have lower value and are considered less critical to your business. They still require management but may not need the same level of focus as items in Categories A and B.
-
- Set Inventory Policies: Based on the category assignments, establish different inventory policies and control measures for each category. For example:
-
- Category A: Implement tighter inventory control measures, such as frequent monitoring, accurate demand forecasting, and maintaining safety stock levels to avoid stockouts.
-
- Category B: Maintain adequate inventory levels based on demand patterns, review replenishment strategies periodically, and monitor closely for any changes in demand or consumption.
-
- Category C: Apply more relaxed inventory management policies. Focus on optimizing inventory turnover, reducing carrying costs, and periodically reviewing the need for certain items.
-
- Monitor and Review: Regularly review and update the ABC categorization based on changing sales patterns, new products, or market dynamics. Conduct periodic audits to ensure that items are appropriately classified and that the inventory policies are effectively implemented.
AME Storage Solutions is your trusted partner for all your storage solutions in UAE. With our extensive range of high-quality warehouse racking and shelving, including pallet racking, mezzanine systems, and shelving units, we ensure optimal space utilization and efficient organization for your warehouse or storage facility. Our dedicated team of experts is committed to delivering exceptional customer service and providing customized solutions tailored to your specific requirements. Whether you’re a small business or a large enterprise, AME Storage Solutions is here to help you maximize productivity, streamline operations, and achieve your storage goals.
Explore our products and take the first step toward a more organized and efficient storage solution. Trust AME Storage Solutions for all your racking and shelving solutions in UAE.
To keep in touch on our activities, follow us on Instagram, Facebook, and LinkedIn.
For more details and services Contact Us
Please visit our previous blog by clicking here.