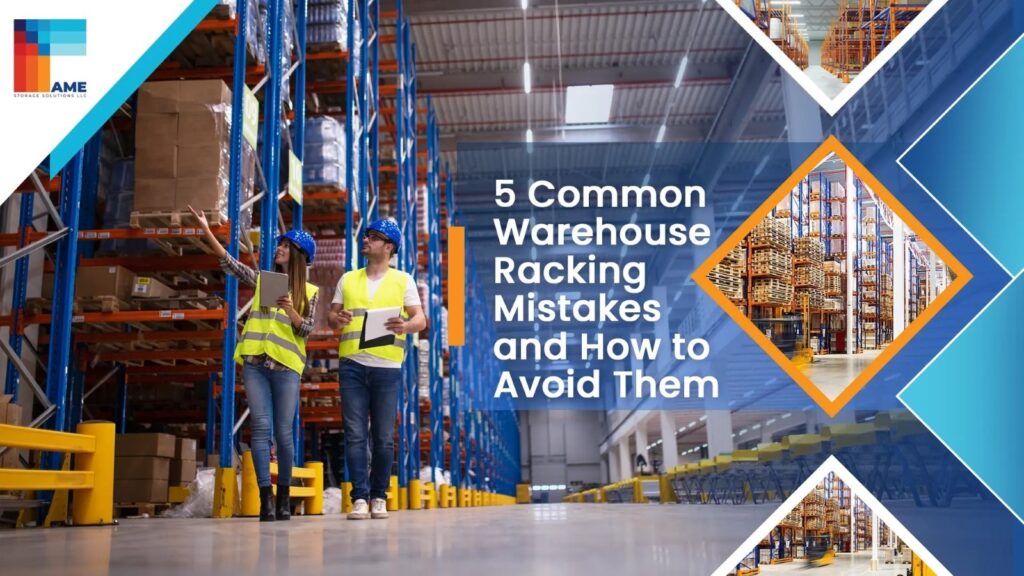
As per the opinion of storage solutions in UAE, an efficient warehouse racking system is essential for optimizing storage space, streamlining operations, and ensuring the safety of warehouse staff. However, as per analysis of experts from storage solutions in UAE , there are several common mistakes that may occur when implementing and managing warehouse racking systems. These mistakes can lead to inefficiencies, compromised safety, and increased operational costs. By understanding these common pitfalls, warehouse managers can take proactive measures to avoid them and create a well-organized, productive, and secure racking environment. Here, we will discuss five common warehouse racking mistakes and provide insights on how to prevent them. By addressing these issues, you can enhance your warehouse’s productivity, safety, and overall operational efficiency.
Overloading racking
Overloading racking system is a common mistake that can have severe consequences in a warehouse environment. These mistakes are very commonly seen in racking system in Dubai. When racks are loaded with more weight than they can handle, it not only compromises the structural integrity of the racks but also poses significant safety risks to workers. Here are some important points to consider avoiding overloading the rack:
-
- Understand Load Capacity: The first step in preventing overloading is to understand the load capacity of your racks. Each racking system has a specified load capacity, which should be clearly indicated by the manufacturer. It is important to educate your warehouse staff about these load limits and ensure they are aware of the consequences of exceeding them.
-
- Know Your Inventory: Have a clear understanding of the weight and dimensions of the items you store in your warehouse. It is essential to accurately weigh and measure each item to determine its impact on the rack’s load capacity. Regularly update your inventory records to reflect any changes in product weights or sizes.
-
- Train Employees: Provide comprehensive training to your warehouse staff on proper loading techniques and weight distribution. They should understand the importance of following load capacity guidelines and be able to identify signs of overloading. Training should include topics such as evenly distributing weight, avoiding concentrated loads, and recognizing warning signs of overloaded racks.
-
- Use Load Labels: Clearly mark the load capacity of each rack with load labels. These labels should be visible and easily understandable to anyone loading or accessing the racks. Load labels serve as a reminder to employees and provide a quick reference for the maximum weight allowed on each shelf or level.
-
- Implement Weight Verification Procedures: To ensure accurate weight distribution and prevent overloading, implement procedures for verifying the weight of items before they are placed on racks. This can involve using calibrated scales or weight verification systems to double-check the weight of pallets or individual items.
-
- Conduct Regular Inspections: Perform regular inspections of your racking system to identify any signs of stress, damage, or deflection. Look for bent or cracked beams, loose connections, or any other structural issues. Inspections should be conducted by trained personnel who are knowledgeable about rack safety.
-
- Invest in Load Monitoring Systems: Consider installing load monitoring systems that provide real-time information on the weight distribution within racks. These systems use sensors or load cells to continuously monitor the weight and detect any deviations from the safe load limits. They can provide immediate alerts when overloading occurs, allowing for prompt corrective action.
-
- Communicate and enforce safety procedures. Promote a culture of safety in your warehouse by clearly communicating and enforcing safety procedures. Emphasize the importance of following load capacity guidelines and the potential risks associated with overloading. Encourage workers to report any concerns or observations regarding overloading or structural integrity.
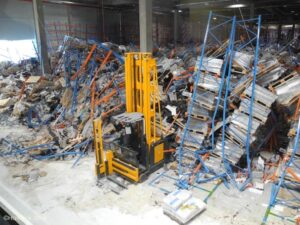
Overloading racking is a serious mistake that can lead to structural failures, inventory damage, and workplace injuries. As per the opinion of storage solutions in UAE , by understanding load capacity, training employees, implementing weight verification procedures, conducting regular inspections, and investing in load monitoring systems, you can significantly reduce the risk of overloading and ensure a safe and efficient warehouse environment. Remember, maintaining safety should always be a top priority in warehouse shelving operations.
Improper installation of racking
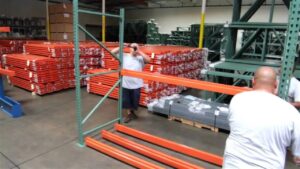
Improper installation of racking is a common mistake that can compromise the stability and safety of the entire warehouse storage system. To avoid this mistake, it is crucial to follow proper installation procedures and guidelines. Here are some important points from expert storage solutions in UAE , to consider avoiding improper installation of racking:
-
- Consult Manufacturer Guidelines: Before installing any racking system, carefully review the manufacturer’s guidelines, instructions, and specifications. Manufacturers provide detailed instructions on how to assemble and install their racking systems correctly. These guidelines may include specific hardware requirements, anchoring instructions, and recommended load capacities. Familiarise yourself with these guidelines and ensure that your installation team follows them meticulously.
-
- Use Trained and Experienced Installers: Racking installation should be carried out by trained and experienced personnel who are knowledgeable about the specific racking system being installed. They should have a thorough understanding of the manufacturer’s instructions and the necessary tools and equipment required for installation. If your team lacks the expertise or experience, consider hiring professional storage solutions in UAE who specialise in racking systems.
-
- Ensure Proper Alignment and Levelling: During installation, pay close attention to the alignment and levelling of the racking components. Improper alignment can result in uneven weight distribution and compromised stability. Use a level and measuring tools to ensure that all uprights, beams, and connectors are aligned correctly. This step is crucial for the overall stability and load-bearing capacity of the racking system.
-
- Secure Anchoring: Properly anchoring the racking system to the floor or walls is vital for its stability and safety. Follow the manufacturer’s recommendations for anchor types, sizes, and quantities. Ensure that the anchors are installed securely and tightened to the specified torque. Anchoring prevents the racking system from tipping or collapsing during loading and unloading operations or in the event of seismic activity.
-
- Regularly Inspect and Maintain: After installation, implement a regular inspection and maintenance program for your racking system. Inspect the system for any signs of damage, including bent or damaged components, loose connections, or signs of excessive stress. Regular maintenance includes tightening bolts and fasteners, replacing damaged parts, and addressing any issues promptly to maintain the integrity of the racking system.
-
- Seek Professional Assistance: If you are unsure about the proper installation of racking or have a complex warehouse layout, it is advisable to seek professional assistance. Engaging experts who specialise in warehouse racking systems can ensure that the installation is done correctly and meets all safety requirements.
-
- Training and documentation: Provide training to your employees on the proper handling and use of racking systems. This includes educating them on load capacities, safe loading and unloading procedures, and how to recognise signs of damage or instability. Develop clear documentation and guidelines that outline the correct installation procedures, safety protocols, and ongoing maintenance requirements. Ensure that all employees involved in warehouse operations have access to this information.
Proper installation of racking systems is crucial for maintaining a safe and efficient warehouse environment. By consulting manufacturer guidelines, using trained installers, ensuring proper alignment and anchoring, conducting regular inspections and maintenance, seeking professional assistance when needed, and providing training and documentation to employees, you can avoid the common mistake of improper installation and ensure the stability and safety of your warehouse racking system. Remember, investing time and effort in correct installation practices will contribute to the long-term success of your warehouse racking operations.
Lack of regular maintenance of racking
Lack of regular maintenance of racking and shelving is a common mistake which is seen in racking system in Dubai, which leads to deteriorating rack conditions, potential failures, and compromised safety in the warehouse. To avoid such mistakes, it is crucial to implement a comprehensive maintenance program for your racking system.

Here are some important points to consider avoiding the lack of regular maintenance of racks:
-
- Establish a Maintenance Schedule: Create a maintenance schedule that includes routine inspections and necessary maintenance tasks. Determine the frequency of inspections based on the usage and conditions of your racking system. Regular inspections can help identify potential issues and address them before they escalate into more significant problems.
-
- Inspect for Signs of Damage: During inspections, pay close attention to signs of damage or wear on the racking components. Look for bent beams, cracked uprights, damaged connectors, or any other visible signs of stress. Inspect the floor beneath the racks for any signs of movement or damage that could affect the stability of the racking system.
-
- Replace Damaged Components: If any damaged or compromised components are identified during inspections, promptly replace them with new ones. Bent or damaged beams, uprights, or connectors can weaken the overall structure of the racking system. Replacing damaged components ensures the integrity and load-bearing capacity of the racks.
-
- Tighten Bolts and Fasteners: Regularly check and tighten bolts, nuts, and fasteners throughout the racking system. Over time, vibrations and movement can cause these connections to become loose, compromising the stability of the racks. Use appropriate tools and follow the manufacturer’s recommendations for torque values when tightening the fasteners.
-
- Ensure Proper Alignment: Check the alignment of the racking system during inspections. Over time, components may shift or become misaligned, affecting the overall stability and load distribution. If misalignment is detected, adjust the racks to restore proper alignment and weight distribution.
-
- Consider load adjustments: As your inventory and storage requirements change, periodically assess the load distribution and adjust accordingly. Some products may be removed or added, resulting in uneven weight distribution across the racks. Ensure that heavier items are properly supported and evenly distributed to maintain the load capacity of the racking system.
-
- Train employees in maintenance procedures: Educate your warehouse staff on the importance of regular maintenance and provide training on how to identify signs of damage or instability. Train them on proper procedures for tightening bolts, inspecting for damage, and reporting any concerns. Encourage employees to be proactive in reporting any issues they observe during their daily operations.
-
- Document Maintenance Activities: Maintain a record of all maintenance activities performed on the racking system. Document inspections, repairs, component replacements, and any other maintenance tasks. This record will serve as a reference for future inspections, allow for traceability, and help track the overall condition of the racking system over time.
-
- Engage Professionals for Structural Assessments: Periodically engage professionals, such as structural engineers or racking system experts, to conduct comprehensive assessments of your racking system. These professionals can evaluate the structural integrity, load capacities, and overall safety of the system. Their expertise can help identify any potential issues that may have been overlooked during routine maintenance.
Regular maintenance of racking systems is vital for ensuring the safety and longevity of the warehouse storage infrastructure. By establishing a maintenance schedule, conducting inspections, replacing damaged components, tightening bolts, ensuring proper alignment, considering load adjustments, training employees, documenting maintenance activities, and engaging professionals for structural assessments, you can prevent the common mistake of neglecting regular maintenance. Expert storage solutions in UAE, says that a well-maintained racking system contributes to a safe and efficient warehouse environment.
Poor inventory management of racking
Poor inventory management of racking and shelving systems is a common mistake that can lead to inefficiencies, wasted space, and difficulty in locating and accessing stored items. To avoid this mistake, it is crucial to implement effective inventory management practices specifically tailored to your racking system. Here are some important points to consider avoiding poor inventory management for storage solutions:
-
- Categorize and label inventory: Establish a clear inventory categorization system that suits your warehouse operations and products. Assign specific locations or zones within the racking system for different categories or product types. Clearly label each location or shelf with the corresponding product information, such as SKU numbers, descriptions, or barcode labels. This helps in quickly identifying and locating items during picking or replenishment processes.
-
- Implement Slotting Strategies: Develop and implement slotting strategies that optimize the storage and retrieval processes. Analyze product characteristics, demand patterns, and order frequency to determine the most appropriate placement of items within the racking system. Consider factors such as size, weight, and picking frequency when deciding on slotting arrangements. Position frequently picked items in easily accessible areas and prioritized popular products for efficient order fulfilment.
-
- Utilize Inventory Management Software: Invest in inventory management software or warehouse management system (WMS) that integrates with your racking system. Such software allows you to track inventory levels, monitor stock movements, and generate real-time reports. Utilize the software’s features, such as automated reorder points and stock rotation reminders, to maintain accurate inventory levels and prevent stockouts or excess inventory.
-
- Conduct Regular Cycle Counts: Perform regular cycle counts to validate inventory accuracy. This involves counting a subset of items within the racking system on a regular basis, comparing the count to the recorded quantities, and investigating any discrepancies. Cycle counting helps identify and rectify inventory discrepancies promptly, ensuring accurate inventory records and minimizing errors in order fulfillment.
-
- Implement First-In, First-Out (FIFO) Principles: For products with expiration dates or shelf-life considerations, implement a first-in, first-out (FIFO) inventory management strategy. Arrange items in the racking system based on their arrival dates, with older items placed in front of newer ones. This ensures that older inventory is used or sold first, reducing the risk of product obsolescence and minimizing waste.
-
- Train Staff on Proper Inventory Handling: Provide training to warehouse staff on proper inventory handling procedures. This includes educating them on accurate recording of inventory movements, following established slotting arrangements, and practicing good housekeeping to maintain organized racks. Train employees on how to use inventory management software effectively and emphasize the importance of timely and accurate data entry.
-
- Conduct Regular Stock Reconciliation: Perform periodic stock reconciliation to compare physical inventory counts with recorded quantities. This helps identify any discrepancies and allows for timely adjustments to maintain accurate inventory records. Use this opportunity to address any issues related to damaged or misplaced items, as well as identify potential improvements in inventory management processes.
-
- Optimize Replenishment Processes: Ensure efficient replenishment processes to avoid stockouts and maintain optimal inventory levels. Monitor inventory levels regularly and establish reorder points to trigger replenishment orders. Streamline the replenishment process by establishing clear procedures for receiving and stocking new inventory, ensuring items are stored in the appropriate locations within the racking system.
-
- Continuously Review and Improve: Regularly review your inventory management processes and seek opportunities for improvement. Analyze data from inventory management software, gather feedback from warehouse staff, and assess key performance indicators (KPIs) related to inventory accuracy, stock turnover, and order fulfillment. Use this information to identify areas for improvement and implement changes accordingly.
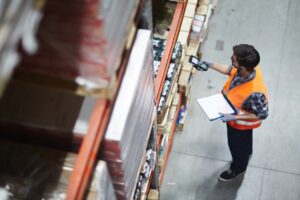
Effective inventory management is essential for maximizing the efficiency of your racking system. By categorizing and labeling inventory, implementing slotting strategies, utilizing inventory management software, conducting regular cycle counts and
Improper use of accessories
Improper use of accessories in racking is a common mistake that can compromise the stability, load capacity, and overall functionality of the racking system, as per the opinion of storage solutions in UAE. Accessories such as pallet supports, wire mesh decking, dividers, and safety clips are designed to enhance the performance and safety of the racking. However, if they are used incorrectly or not at all, it can lead to inefficiencies and safety hazards. To avoid this mistake, it is important to understand the purpose and proper usage of accessories in racking.
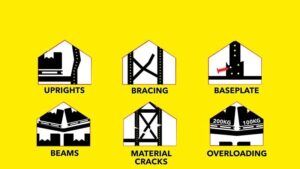
Here are some important points to consider avoiding improper use of accessories in racking system:
-
- Understand Manufacturer Guidelines: Refer to the manufacturer’s guidelines and instructions for the specific accessories you are using. The manufacturer will provide instructions on the correct installation, usage, and load capacities of each accessory. Familiarise yourself with these guidelines and ensure that your warehouse staff follows them accordingly.
-
- Use accessories as intended: Each accessory is designed for a specific purpose. Ensure that you use accessories for their intended use and in the recommended manner. For example, pallet supports are designed to provide additional support to palletized loads, wire mesh decking enhances safety and stability, and dividers help with better organization and separation of products. Avoid using accessories for purposes they are not designed for, as it may compromise the structural integrity of the racking system.
-
- Follow Load Capacity Guidelines: Understand the load capacity of the accessories and ensure that they are not overloaded. The manufacturer will provide load capacity ratings for each accessory, and exceeding these limits can result in damage to the accessory, as well as the racking system. Educate your warehouse staff on load capacity guidelines and enforce proper weight distribution to prevent overloading.
-
- Proper Installation: Follow proper installation procedures for accessories to ensure they are securely attached to the racking system. Improper installation can result in accessories becoming loose or dislodged, posing safety risks and potentially damaging stored inventory. Train your staff on the correct installation techniques and periodically inspect accessories to ensure they are properly installed and in good condition.
-
- Regular Inspections: Conduct regular inspections of the accessories in your racking system to identify any signs of damage, wear, or improper usage. Look for bent or broken accessories, loose connections, or any other visible issues. Inspections should be carried out by trained personnel who can identify potential risks and take appropriate action to address them.
-
- Train Employees on Proper Usage: Provide training to your warehouse staff on the proper usage of accessories in racking. Educate them on the specific functions and benefits of each accessory and how to use them correctly. Emphasize the importance of following manufacturer guidelines and load capacity limits. Regular training sessions and refresher courses can help reinforce proper usage practices.
-
- Communicate Safety Procedures: Promote a culture of safety in your warehouse by clearly communicating and enforcing safety procedures related to accessory usage. Emphasize the importance of using accessories correctly and the potential risks associated with improper usage. Encourage employees to report any concerns or observations regarding the usage of accessories.
-
- Document Usage and Maintenance: Maintain records of accessory usage and maintenance activities. Keep track of when accessories were installed, any maintenance or repairs performed, and any changes made to the racking system. This documentation can help with tracking the lifespan of accessories, identifying patterns of wear or damage, and ensuring timely replacements or repairs.
Major storage solutions in UAE is of the opinion that, proper use of accessories in racking system is crucial for maintaining a safe and efficient warehouse environment. By understanding manufacturer guidelines, using accessories as intended, following load capacity guidelines, ensuring proper installation, conducting regular inspections, training employees on proper usage, communicating safety procedures, and documenting usage and maintenance activities, you can avoid the common mistake of improper use of accessories in storage solutions. Remember, the correct usage of accessories enhances the functionality and safety
Storage Solutions In UAE
AME Racking is your trusted partner for all your storage solutions in UAE. With our extensive range of high-quality racking and shelving solutions, including pallet racking, mezzanine systems, and shelving units, we ensure optimal space utilization and efficient organization for your warehouse or storage facility. Our dedicated team of experts is committed to delivering exceptional customer service and providing customized solutions tailored to your specific requirements. Whether you’re a small business or a large enterprise, AME Storage Solutions is here to help you maximize productivity, streamline operations, and achieve your storage goals.
Explore our products and take the first step toward a more organized and efficient storage solution. Trust AME Storage Solutions for all your racking and shelving solutions in UAE.